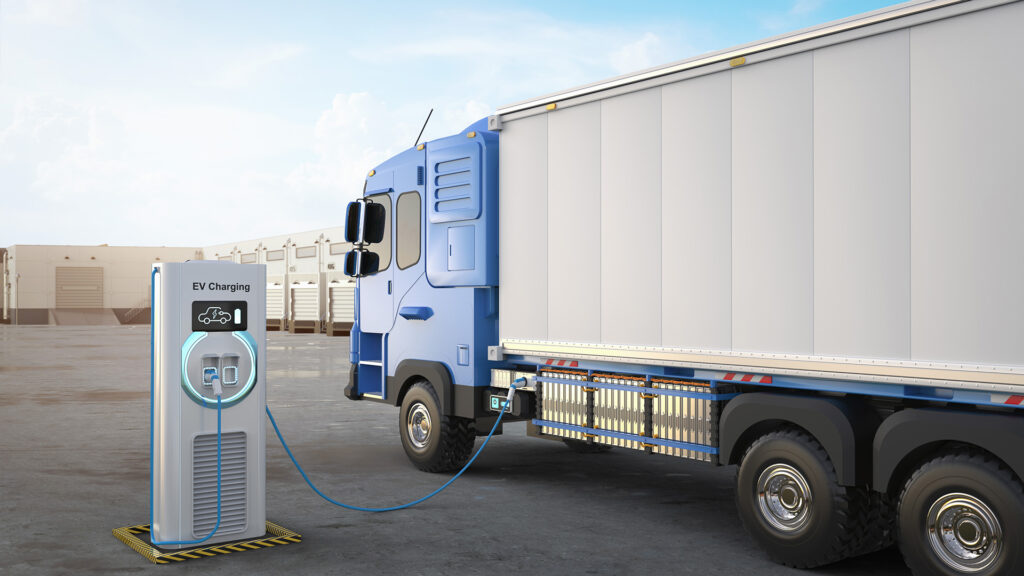
Electric vehicle (EV) capabilities have come a long way over just a few years, and EVs are quickly overtaking their gas-driven counterparts. Researchers make clear that investments in EVs have surged since 2020. That’s why the transformation of US roadways, with respect to EV technologies, is no longer a matter of “if”, but “when.”
The shifting general consumer trends are interesting, but we find ourselves far more curious about the applications of EV technology for large commercial vehicles, as that sector faces much steeper technological barriers to widespread adoptions.
This article gives an overview of most important challenges and opportunities for medium- to heavy-duty electric vehicle (MHDEV) manufacturers and strategic pointers to drive their business for the coming years.
The 2020s as a Critical Decade for Medium- to Heavy-Duty Electric Vehicles
A medium- to heavy-duty electric vehicle is defined as Class 4-8 vehicles in the Gross Vehicle Weight Ratings (GVWR) system. These vehicles are “heavier than their light-duty counterparts, pull heavier loads, and have tougher duty cycles.” They include vehicles such as buses and trams, along with delivery vans, semi-trucks, and other vehicles designed to carry heavy-duty equipment.
The demand for electric vehicles is rising globally. According to a recent report from the International Energy Agency, over 10 million electric vehicles were sold across the world in 2022, and of those sales, 66,000 were electric buses and another 60,000 were medium- and heavy-duty trucks. Experts only predict those numbers to rise in the coming years.
Medium- to heavy-duty vehicles, the second largest contributor to greenhouse emissions, can also be a promising solution to decarbonizing the transportation sector. As a result, there is stakeholder commitment in helping grow the electrification of the MHDEVs.
How US Manufacturers Involved with EV Technologies and Transport Should Move Forward
While stakeholder commitments and growing investments in medium- to heavy-duty electric vehicles is a positive sign for EV manufacturers, many unknowns persist, making strategic decisions about investments in MHDEVs fraught with uncertainties.
With so much influx around the future of transportation technologies, those who don’t plan for the future are sure to get left behind. If you’re a manufacturing or engineering firm in the EV sector, here are five things you should be paying attention to:
- Current EV Infrastructure & Its Future State
EV charging station issues are a notorious problem facing wider adoption of EV technologies throughout the United States. This is especially true for MHDEVs that face a special problem due to their long travel durations and/or heavy loads that require much larger batteries. This means they must depend on private charging depots, public charging facilities, and on-route charging, in addition to more efficient charging technologies.
For manufacturing & transportation companies, the industry is already poised for a robust infrastructural rollout. There has been rapid deployment of publicly-available fast chargers along motorways to enable longer journeys, thanks to the National Electric Vehicle Infrastructure Formula Program (NEVI). According to the National Renewable Energy Laboratory (NREL), commercial charging stations are already being designed to charge large, commercial EVs in less time and money thanks to the development of megawatt-charging systems.
In the ever-changing landscape of electric vehicle (EV) charging technologies and policies, having enterprise-grade EV experts by your side can be a game-changer for manufacturers. They can help you navigate through complex and rapidly-evolving technologies and policy landscapes. They can even help manufacturers take full advantage of rapidly-growing federal and state incentives.
- Evolving Technologies & Impacts
The range and efficiency of EVs largely comes down to the batteries that power them. Not only are there multiple battery options for EVs, but the battery technologies are expanding rapidly, including the rising capabilities of charge-sustaining electric vehicles, which have an “unlimited range with in-route charge,” as well as new materials, new approaches, and wireless charging options. The goal of the new technologies is to improve energy density, reduce weight, and improve battery performance.
Given that battery technologies are evolving rapidly, each change has implications for equipment and vehicle configurations. The most efficient product and process solutions will be tailored to the energy cycle demands of the MHDEVs in question. Minimizing the size of the installed battery, while still ensuring a full day’s operation, would be key in designing and manufacturing cost-effective and efficient EVs.
In addition, innovative design practices, such as utilizing lightweight materials and implementing regenerative braking systems for energy recapture, will play a crucial role in improving energy efficiency of vehicles, while extending their driving range.
- Higher Costs of Production
The higher the power demands on the EV, the bigger the battery. The bigger the battery, the more expensive the vehicle. For instance, Tesla Semi has a battery pack that alone weighs over 11,000 pounds! That means medium- to heavy-duty electric vehicles can come with a steep price tag.
Bigger and heavier batteries are not the only reason for high costs of MHDEVs production. Start-up costs associated with setting up of MHDEVs production plants are also steep. This is due to higher capital investments needed for the development of advanced and reliable battery technology that feed into supplier costs, investment in new manufacturing processes that are different from processes suited to gas-powered vehicle production, and a skilled workforce designed for more efficient assembly requirements.
By collaborating with industry experts, taking advantage of government subsidies to reduce upfront costs, and scaling of operations, manufacturers can create enhanced efficiencies and ultimately push down the price tags associated with EV production.
- Complex Supply Chains
The EV battery supply chain is complex and dispersed throughout the world. It is also unpredictable due to unavoidable geo-political and economic complexities.
Upstream challenges include issues of capacity. Lithium and cobalt requirements to meet the ever-increasing battery average capacity are expected to surpass the amount of reserves. The EV supply chain is also wrought with component shortages, shipping delays, and inefficient production processes.
Merkur, as a leading engineering solutions firm specializing in transportation & manufacturing solutions, recommends flexible design standards, reliance on a diversified supplier network, opting for local resources, and partnering with strategic engineering solutions experts early in your strategic process, so they can help you stay ahead of supply chain complexities, optimize your costs, and save you time.
- Energy Availability and Grid Capacity.
One of the driving benefits of electric vehicles is their ability to reduce reliance on fossil fuels. Unfortunately, while fossil fuels serve as on-demand energy sources, renewable sources of energy are less reliable. The electrification of vehicles is only going to increase the load on the electric grid. According to the EV Hub, the ongoing electrification of MHDEVs is expected to increase U.S. daily energy consumption by 140,000 megawatt-hours per day by 2030!
For that reason, our electric grids need a major tune-up. Currently, energy storage capabilities are lacking, meaning that for the time being, we will require use of fossil fuels to supply energy to the grid as needed.
Policy shifts and technological improvements to support improved load management, effective vehicle-to-grid integrations and a move to a more dispersed grid are all steps in the right direction that can meet local demands and provide a boost to the EV markets. Manufacturers must stay abreast of these policy shifts that may impact their manufacturing choices in the years to come.
Merkur as Your Partner in Strategic Positioning into the Future
At Merkur, our teams of innovators and experts are ready to support you with deep industry insights, industry-leading technical knowledge, and more. See how Merkur, as an end-to-end design & build partner, helped design and build a 1 million sq. ft. production plant for zero-emission vehicles.
For US-based manufacturers aiming to make strides in the EV space, partnering with the right stakeholders will make all the difference. We’re ready to work with you. Give us a call or schedule a consultation through our website today.